
Construction Project Management Solutions
No matter the complexity of the build, our expert team will ensure cost, time, quality and construction risks are managed, to deliver your project on schedule, within budget and to the highest standard.

Coles Supermarkets, Automated High-Bay Distribution Centres
-
Development of detailed technical design documentation and architectural plans​.
-
Property procurement via a competitive developer tender and selection process​.
-
Negotiation of Agreement for Lease.
-
Project management of the delivery of the facility (inclusive of integration of automation).
​
-
Value engineered the design brief and ran the property procurement process concurrently in NSW and QLD to create additional negotiating leverage.
-
Negotiated and finalised Agreement for Lease within a timeframe of only 4 weeks to meet Coles critical date.​
-
Sourced Coles a facility aligned to their exact specifications within their desired location​.
-
Reduced the initial lease term by 6 years​.
-
Integrated automation into the base building definition significantly reducing future make good costs.
PFD Foods Distribution Centre and Seafood Processing Facility
-
PFD Foods operated 3 separate assets in Knoxfield and had an intent to consolidate their operations under one roof​.
-
Existing premises occupied by PFD Foods required significant upkeep and maintenance whilst also being functionally obsolete​.
-
PFD Foods had a rapidly growing customer base, additional storage to meet current and future forecasts was required.
-
Strict food standards.
-
Significant rainwater harvesting was required to service the large refrigeration plant.​
-
Strict water sensitive urban design controls.
​
-
Developed a performance specification technical design brief from an earlier project concept which achieved savings through competitive tender while also delivering a class leading result.​
-
On time and on budget delivery of the facility.​
-
Delivery of a brand new, class leading seafood processing facility enabling rapid expansion of the seafood business.​
-
New facility sized to accommodate significant business growth into the future.​
-
Office facilities to support warehouse management and sales functions.

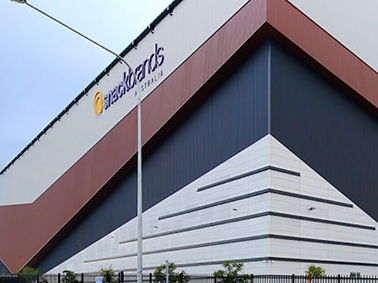
Snack Brands High-Bay Distribution Centre
-
Occupied 6 manufacturing and distribution centres in Western Sydney.
-
Wide ranging lease expiry date profile on the 6 occupied facilities.
-
Distribution centre lease expiries were fast approaching.
-
Establishing true day to day operating costs as a result of the supply chain network.
​
-
Undertook an end-to-end operational review looking at multiple business case scenarios to determine the optimum operational model and the consolidation of Snackbrands NSW distribution and manufacturing operations into one central site.
-
A state-of-the-art 40,000 pallet ASRS automated solution with future expansion for 10,000 pallets was chosen.
-
Coordinated the manual and automation design, concepts and articulated to Snackbrands the full ASRS costing and associated benefits.
-
Provided support to Snackbrands in the detailed design, implementation (until go live) and commissioning phases for the automation solution to ensure a smooth transition.
-
Managed the review and evaluation of tender responses from the automation providers before advising and negotiating on behalf of Snackbrands.
-
Project management of the delivery of the facility integrating the automation into the base building and delivering the facility on time and within budget.